In January 2020, Sciensoria delivered a quality control device for electrical welds on car chassis ordered by the Excelcar platform. This order is part of a research program among the 24 research programs launched in cooperation with PSA Automobiles with the aim of modernizing the design and production of its cars. Increased quality control and Industry 4.0 are on the menu.
Located next to the PSA site in La Janais, Bruz (Ille et Vilaine), the EXCELCAR platform was founded in 2015 at the initiative of the iD4CAR competitiveness cluster and players from the industrial and academic ecosystem in order to industrialize innovation, thanks to an industrial Fablab approach and means at scale 1.
The product is directly intended for the quality check and validation operations on the cars produced by the PSA Automobiles group. The control time of a weld spot is of the order of a few seconds, compared to a few minutes offered by an ultrasonic device. In addition, its operating principle based on the phenomenon of eddy currents makes it possible to control the assemblies of thin sheets, a field where the ultrasound technique encounters difficulties.
The device, from the Z-Scope * 7W series (W for “weld”), is intended for the quality control of steel-steel, steel-aluminum or aluminum-aluminum assemblies. It can detect the “zinc glue” situation where a weld spot can appear good seen by a thermal camera but in reality the connection between the metal sheets is very poor.
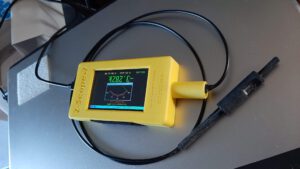
The Z-Scope*7W, eddy current instrument for spot welding testing
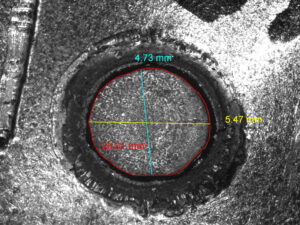
A good weld spot: the connection between the 2 metal sheets is big enough
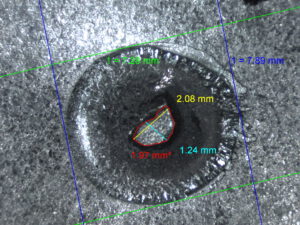
A poor weld spot (zinc glue). Very few melt metal can be found inside the weld spot
As a reminder, the non-destructive testing of an electric welding point by ultrasound requires several minutes. Recently, chisel checks were still carried out on the assembly lines. The eddy current technique is advantageous in more than one way:
- Very fast
- Does not require coupling gel like ultrasound
- Easy to position
- Non-destructive